Aluminum-plastic composite board is a new decorative material. Because of its strong decorative, colorful, durable, light weight and easy to process, it has been rapidly developed and widely used at home and abroad.
In the eyes of the layman, the production of aluminum-plastic composite board is very simple, but in fact it is a very high technical content of new products. Therefore, the quality control of aluminum-plastic composite panel products has certain technical difficulty.
The following are the factors affecting the 180° peel strength of aluminum - plastic composite panel:
The quality of aluminum foil itself is a problem. Although this is a relatively hidden problem, it has been reflected in the quality of aluminum-plastic panels. On the one hand, it is the heat treatment process of aluminum. On the other hand, some aluminum panels and manufacturers use recycled aluminum waste without strict quality control. This requires the aluminum plastic board manufacturer to conduct a comprehensive assessment of the material manufacturer, establish business contacts and ensure the quality of materials after determining qualified subcontractors.
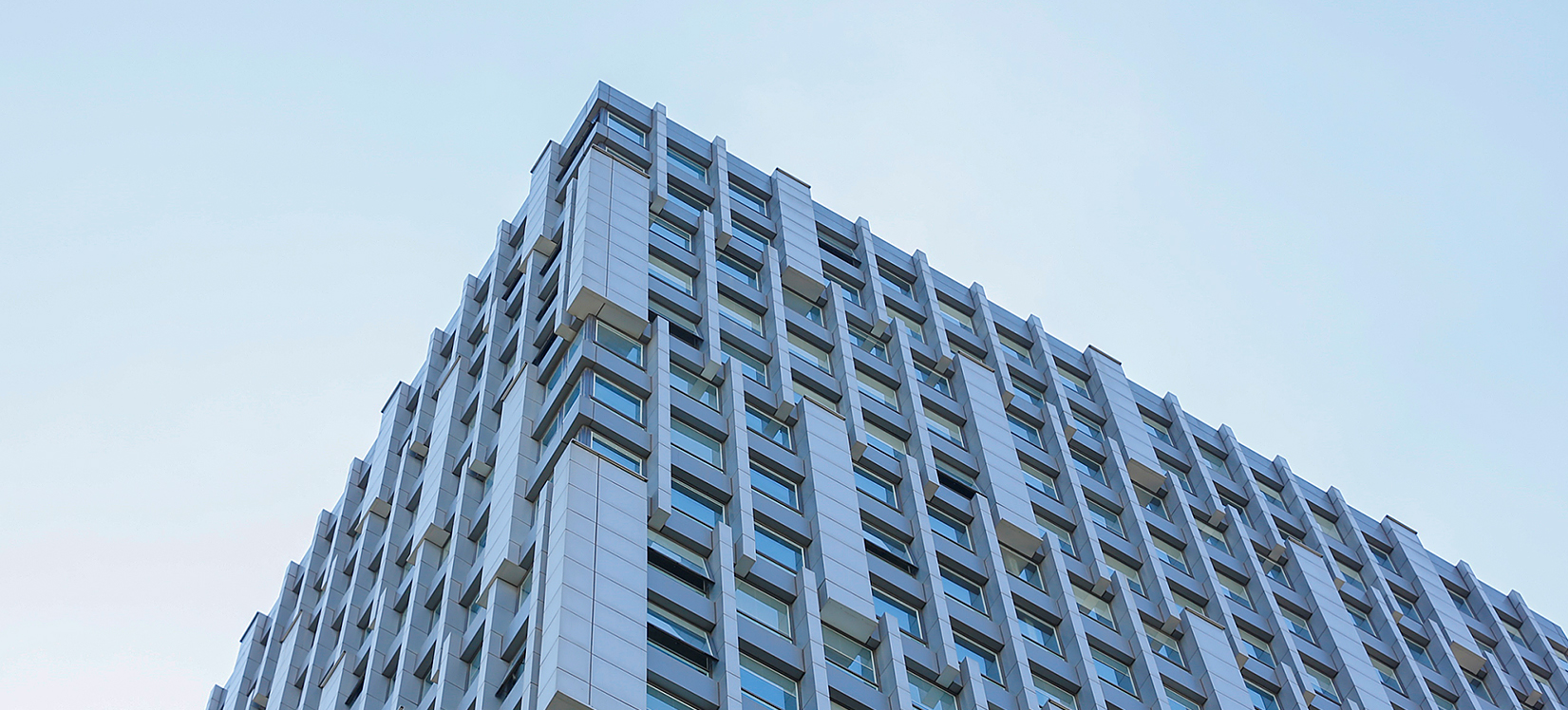
The pretreatment of aluminum panel. The cleaning and lamination quality of aluminum panel are directly related to the composite quality of aluminum plastic panel. The aluminum panel must be cleaned first to remove oil stains and impurities on the surface, so that the surface forms a dense chemical layer, so that the polymer film can produce a good bond. However, some manufacturers do not strictly control temperature, concentration, treatment time and fluid updates during pretreatment, thus affecting cleaning quality. In addition, some new manufacturers use the aluminum sheet directly without any pretreatment. All of these will inevitably lead to poor quality, low 180° peel strength or instability of the composite.
Selection of core materials. Compared with other plastics, polymer films bond best to polyethylene, are affordable, non-toxic and easy to process. So the core material is polyethylene. To reduce costs, some small manufacturers choose PVC, which has poor bonding and produces deadly toxic gases when burned, or choose PE recycled materials or use PE raw materials mixed with the substrate. Due to different PE types, aging degrees and so on, this will lead to different compounding temperatures, and the final surface compounding quality will be unstable.
Choice of polymer film. Polymer film is a kind of adhesive material with special properties, which is the main factor affecting the quality of composite materials. The polymer film has two sides and is made up of three co-extruded layers. One side is bonded with metal and the other side is bonded with PE. The middle layer is PE base material. The properties of both sides are completely different. There is a big difference in material prices between the two sides. Materials related to aluminum panel workshops need to be imported and expensive. The material mixed with PE can be manufactured in China. Therefore, some polymer film manufacturers make a fuss about this, using a large amount of PE molten material, cutting corners and earning huge profits. The use of polymer films is directional and the front and back cannot be replaced. Polymer film is a kind of self-decomposition film, incomplete melting will lead to false recombination. Early strength is high, the time is long, the strength is reduced by weathering, and even bubbles or gum phenomenon appears.
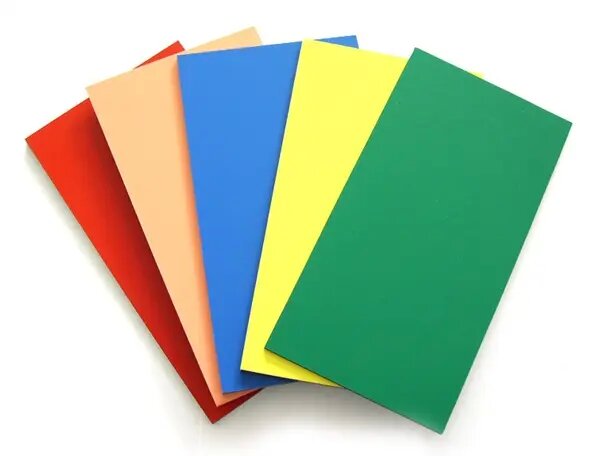
Post time: Jul-22-2022